
- Products
- Solutions
- Learn
- Partner
- Try Now
The holiday season, which is traditionally thought to begin November onwards, is the season of festivities, thanksgiving and coming together. For all economic intents and purposes, the season is also the time for distributing gifts, making new purchases for the coming year and the perfect excuse for letting loose! In 2013, the average amount consumers planned to spend, just for gifts during the holiday season was $801!
This translates into a huge volume of sales during this time and thus, a huge logistical challenge for Supply Chain Management!
Let’s put the holiday season in perspective. The holiday season can represent up to 23.3% of all retail industry sales. For some retailers, the season’s sales can add up to as much as 40% of annual sales! (Source: Derby)
Clearly, the volume of sales is huge. One might wonder how much of this shopping is done online? The share of online sales during the holiday season has been rising constantly. Desktop sales during the holiday season amounted to $32.6 Bn. In 2010. In 2015, the figure went up to $56.43 Bn.! As for Mobile sales, the figure was $7.98 Bn in 2014. In 2015, it went up to $12.65 Bn! (Source: Statista)
The increasing sales in the on-demand space mean that businesses are in for quite the logistical crunch during the holiday season. In fact, many companies proactively prepare for it. For instance, Fed Ex planned to hire 20,000 seasonal workers in 2013 (Source: Derby)! Going by the increasing sales, one can expect even this figure to spike this year.
Both retailers and carriers will have to prepare for the onslaught of consumption that is to come in the following couple of months. For the retailers, stocking up to an optimal degree is the key – without being short-handed or over-burdened. Gauging the optimal amount is the hard part. Through Analytics and Metrics, as well as through Customer Relationship Management, it is possible to make a somewhat accurate prediction.
For Carriers, the challenge is much more complex. It requires fortifying the last-mile, adding to the field workforce, amping up management skills and ensuring efficiency throughout the process of delivery from the warehouse till the destination. Here are some of the specific logistical challenges you may witness this holiday season:
Last Mile Challenges: The Last Mile is the most important part of the supply chain. It is the absolute front-end and is often called the ‘Moment that Matters’ in e-commerce parlance. Last-Mile challenges may be broken down into many micro-challenges. But the essence of it is that optimizing the final delivery of goods to the customer can help you manage up to 30% of the entire cost of the chain! During the Holiday season, it is the Last-Mile which will witness the most chaos. Therefore, it is absolutely imperative to ensure that this phase is appropriately planned for beforehand. Read the dedicated article on Last-Mile Challenges for an in-depth perspective.
Minimizing Reverse Logistics: Reverse Logistics refers to the returning of goods after delivery. 56% of Americans receive unwanted gifts during holidays. 36% of them end up returning them! (Source: Derby). The loss borne because of reverse-logistics can be large during the holiday season. In addition to simply not liking the gift, customer nuances like incorrect address, remote locations, unavailability of the customer to receive the package, etc. can add to the situation and thus become causes of inefficiency in the supply chain.
Types of Goods: Occasionally, even the type of goods can make add to the challenges of last mile delivery. For instance, toxic, fragile, perishable or flammable items call for more planning.
Managing a Larger Workforce: During the Holiday season, all carriers and retailers will need many more employees than usual. For carriers, this means an even bigger workforce on field than before. That is quite the managerial challenge! To manage a larger delivery workforce, map-based tracking, streamlined app- and dashboard- interfaces for communication of relevant details, etc. are imperative. These tasks require sophisticated computational skills, which are simply too much for one human mind.
Proximate Centers: The common practice these days is to have huge, central warehouses as distribution center+s for delivery. Especially during the holiday season, this can prove to be a huge mistake. The smarter thing to do is increasing the number and the spatial spread of distribution centers, so that the supply chain doesn’t get clogged up. By focussing on areas of highest concentration, both delivery and return times are reduced and the costs of fuel are minimized.
Optimization Techniques: Efficient management of the supply chain boils down to optimizing the on-the-ground delivery process. Inefficient routes are the cause of poorly managed time and fuel costs for the business and avoidable delays for the customer. During the holiday season, the potential wastage and thus, the potential savings will be especially huge! Route Optimization ensures that time and fuel costs become time and fuel savings. Algorithms ensure that drivers complete most deliveries in the least amount of time and burning the least amount of fuel by computing variables like: driver availability, location proximity, delivery windows, traffic conditions, local regulations, minimum and maximum order load, weight capacity, etc.
Tookan is a sophisticated system designed to optimize the supply chain through technological innovations and software-solutions. Perhaps it can help you take the edge off this holiday season?
Subscribe to stay ahead with the latest updates and entrepreneurial insights!
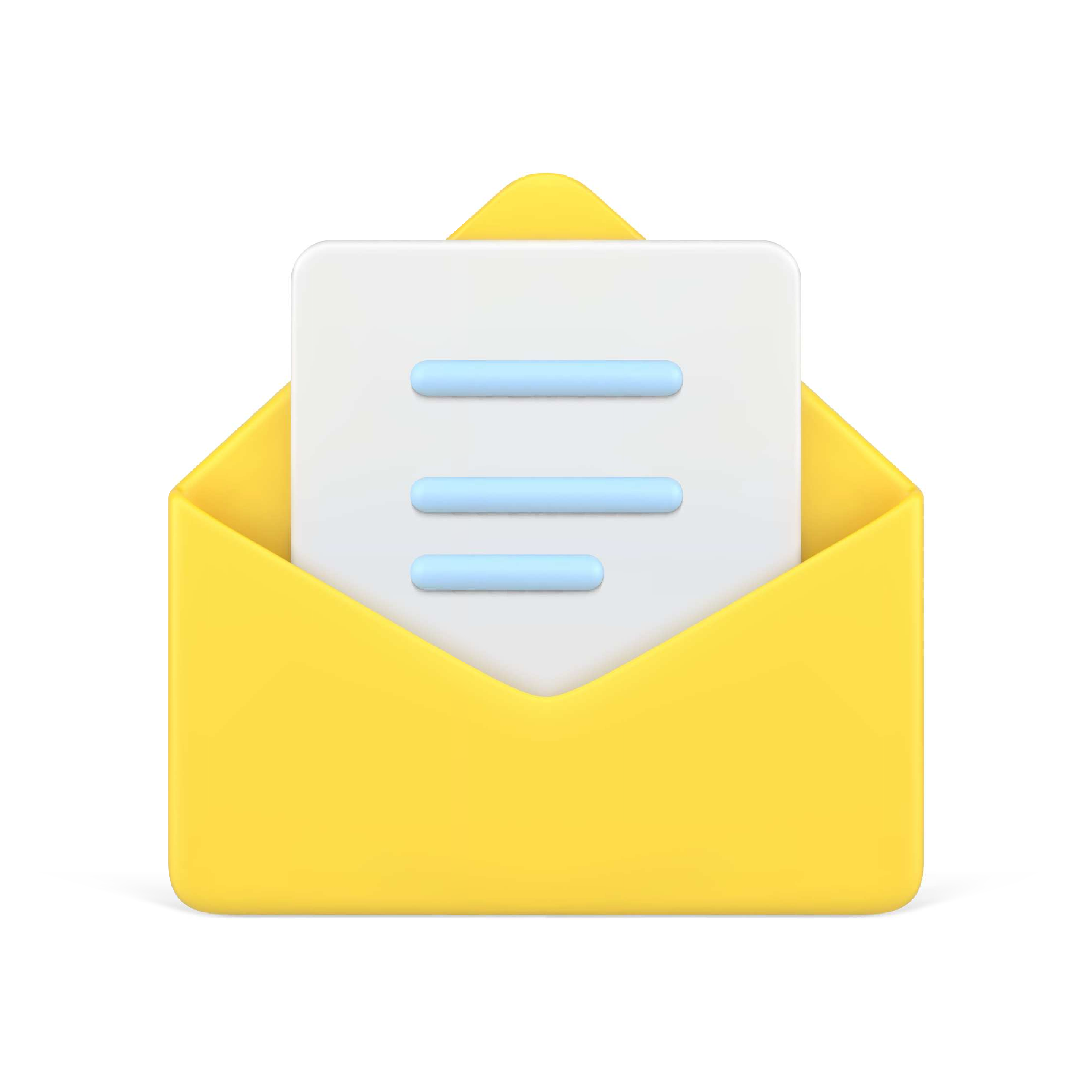
Subscribe to our newsletter
Get access to the latest industry & product insights.